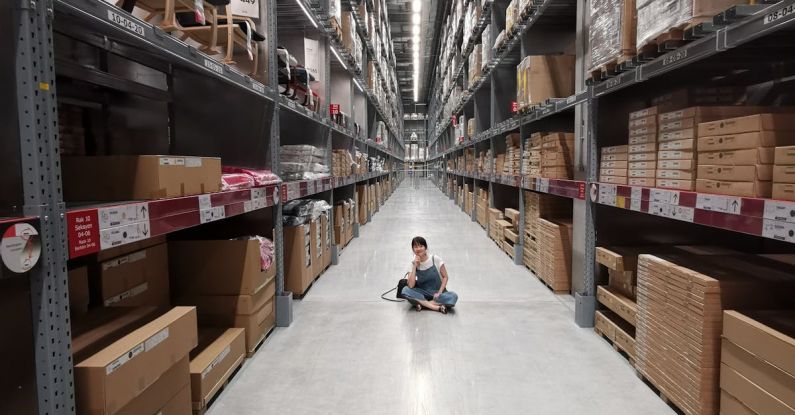
Managing inventory effectively is crucial for any business, regardless of its size or industry. Inventory management involves overseeing the flow of goods from the moment they are acquired to the moment they are sold. By implementing best practices in inventory management, businesses can optimize their operations, reduce costs, improve customer satisfaction, and ultimately increase profitability.
Understanding Demand Patterns
One of the key aspects of effective inventory management is understanding demand patterns. By analyzing historical sales data and trends, businesses can accurately forecast demand for their products. This allows them to maintain optimal inventory levels, prevent stockouts, and reduce excess inventory. Utilizing inventory management software that offers forecasting capabilities can help businesses make informed decisions about how much stock to order and when to replenish it.
ABC Analysis
ABC analysis is a technique used to categorize inventory based on its value and importance. Items are classified into three categories: A, B, and C. Category A includes high-value items that contribute significantly to revenue, but may represent a small percentage of the total inventory. Category B consists of moderately priced items with moderate importance, while Category C includes low-value items that are less critical to the business. By classifying inventory in this way, businesses can prioritize their efforts and resources on managing high-value items more effectively.
Just-In-Time (JIT) Inventory Management
Just-In-Time (JIT) inventory management is a strategy that involves receiving goods only when they are needed, rather than keeping large quantities of inventory on hand. This approach helps businesses reduce storage costs, minimize the risk of dead stock, and improve cash flow. However, implementing JIT inventory management requires careful coordination with suppliers to ensure timely deliveries and a reliable supply chain.
Safety Stock
Safety stock is a buffer of extra inventory that businesses maintain to protect against unexpected fluctuations in demand or supply chain disruptions. By setting appropriate safety stock levels based on factors such as lead times, demand variability, and supplier reliability, businesses can prevent stockouts and maintain high service levels. While carrying too much safety stock can tie up capital and increase storage costs, having too little can result in lost sales and dissatisfied customers.
FIFO and LIFO
FIFO (First-In, First-Out) and LIFO (Last-In, First-Out) are two common methods of inventory valuation. FIFO assumes that the oldest inventory items are sold first, while LIFO assumes that the newest items are sold first. Each method has its own implications for inventory costing, tax implications, and financial reporting. Choosing the most appropriate method for your business depends on factors such as inventory turnover rates, pricing trends, and tax considerations.
Real-Time Monitoring
Implementing real-time monitoring tools can provide businesses with visibility into their inventory levels, sales performance, and supply chain activities. By using barcoding, RFID technology, or inventory management software, businesses can track their inventory in real-time, identify inefficiencies, and make data-driven decisions. Real-time monitoring also enables businesses to respond quickly to changes in demand, reduce stockouts, and improve overall operational efficiency.
Vendor Management
Effective vendor management is essential for maintaining a reliable supply chain and minimizing lead times. By establishing strong relationships with suppliers, businesses can negotiate favorable terms, ensure on-time deliveries, and collaborate on demand forecasting. Regular communication with vendors, performance evaluations, and continuous improvement initiatives can help businesses streamline their supply chain operations and reduce inventory holding costs.
Continuous Improvement
Continuous improvement is a fundamental principle of successful inventory management. By regularly reviewing and optimizing inventory processes, businesses can identify inefficiencies, reduce costs, and enhance customer satisfaction. Implementing lean practices, conducting regular inventory audits, and soliciting feedback from stakeholders can help businesses identify areas for improvement and implement corrective actions.
In conclusion, effective inventory management is essential for businesses to operate efficiently, meet customer demands, and achieve long-term success. By implementing best practices such as understanding demand patterns, using ABC analysis, adopting JIT inventory management, maintaining safety stock, valuing inventory using FIFO or LIFO, monitoring inventory in real-time, managing vendors effectively, and continuously improving operations, businesses can optimize their inventory management processes and drive competitive advantage in the marketplace.